Functional Safety Process
The implementation of functional safety development procedures within the automotive industry context adheres to the IATF 16949 and ISO26262 standards. The incorporation of functional safety procedures into Richtek automotive development process is paramount in meeting industry standards and ensuring the safety and reliability of our products. By aligning with APQP (Automotive Product Quality Planning), safety plan, implementing safety analysis, confirmation measures, and safety case documentation, we have established a robust foundation for functional safety in our projects.
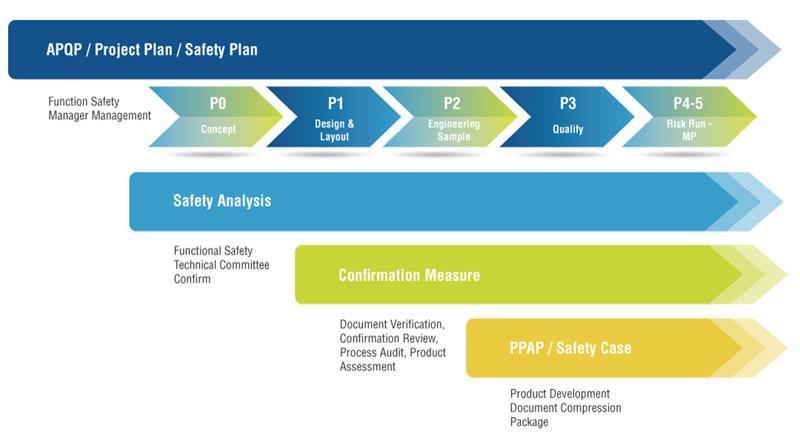
APQP/Project Plan/Safety Plan:
The foundation of the functional safety development process is built upon the IATF 16949 and ISO 26262 standard. Our project planning and safety plans are aligned with the Automotive Product Quality Planning (APQP) framework, a comprehensive quality development plan for automotive products. This ensures that safety considerations are integrated into all stages of the project.
Phase 0 - Concept:
The concept phase is the stage with the highest demand for precision, as it is prone to human errors. This phase involves several key activities:
- Defining the roles of each participant.
- Gathering safety requirements from customers.
- Proposing the system's security concept.
- Reviewing the entire process and safety plan to ensure component readiness for design.
Phase 1 - Design and Layout:
The design phase serves to validate all functional aspects. Main activities include:
- Managing all work related to safety cases.
- Releasing the safety plan.
- Executing security designs that align with the assumed system security concept.
- Conducting Failure Mode and Effects Analysis (FMEA) to minimize common faults between IC functionality and safety mechanisms.
- Performing quantitative safety analysis (FMEDA) to ensure IC design meets functional safety indicators (PMHF, SPFM, and LFM).
- Ensuring all development tools are classified and compliant with ISO 26262 standards.
- Conducting hardware impact analysis and risk assessment if the project involves IP usage.
- Verifying diagnostic effectiveness defined in quantitative safety analysis through simulations.
- Analyzing results of simulations on single point faults and common faults, including package fault analysis and qualitative analysis.
- Managing the process of auditing safety cases through an internally independent team.
Phase 2 - Engineering Samples:
- The phase involves the process of acquiring components. Manage outsourced manufacturer compliance with automotive grade requirements. This information is verified by the functional safety manager, with any deviations requiring immediate review.
- Quality verification of all safety design mechanisms and their related diagnostic scope.
- Completion of component testing and validation through design verification and confirmation stages.
- Testing covers Alpha-site electrical verification, AEC-Q100 package reliability certification, and Automated Test Equipment (ATE) production testing.
- Internal independent team confirmation and review of safety case and process management.
Phase 3 - Quality:
- All safety design mechanisms and their related diagnostic scope fall within the quality verification scope.
- Issuing comprehensive AEC-Q100 reliability certification reports.
- Updating safety manuals and safety analysis reports.
- Evaluating whether functional safety design meets system design definitions and ATE production testing (CP/FT).
- Third-party functional safety assessment to ensure the designed safety conforms to product planning and assumed system applications.
- Internal independent team reviewing safety cases, completing the safety case after approval.
Phase 4 - Risk Run Production:
- Following execution of all monitoring and assessment tests as per automotive development process standards and evaluating test coverage, the product can move into mass production.
- Functional safety manager and designated collaborators confirm all safety-related reviews, along with required assessments or tests.
- Documenting all safety arguments within the safety case, archived for more than 15 years.
- Internal independent team conducting functional safety certification and reviewing functional safety cases before completing and releasing the safety case for the product to enter mass production.
Phase 5 - Mass Production:
- With certification and achieving production quantities, the product can enter mass production.
Safety Analysis:
To ensure the robustness of our safety measures, all functional safety analysis documents have undergone a rigorous review process by an independent central unit. This harmonized safety audit includes critical analyses such as Failure Modes and Effects Analysis (FMEA), Fault Tree Analysis (FTA), Design Failure Analysis (DFA), and Failure Mode, Effects, and Diagnostic Analysis (FMEDA).
Confirmation Measure:
Each stage of the development process, from P0 to P5, conforms to safety measures requirements. All procedures, ranging from requirement definition, specification, testing, to production, have undergone thorough verification. Additionally, an internal independent unit has conducted functional safety audits and evaluations of product functional safety design.
PPAP/Safety Case:
The functional safety case framework builds upon the IATF 16949 Production Part Approval Process (PPAP) encompassing all safety arguments and work outputs. These are stored within a dedicated functional safety section in the configuration management system. This approach ensures that all safety-related aspects are traceable and documented, adhering to the highest standards of quality and safety.